What to Consider for a PLC-to-DCS Migration
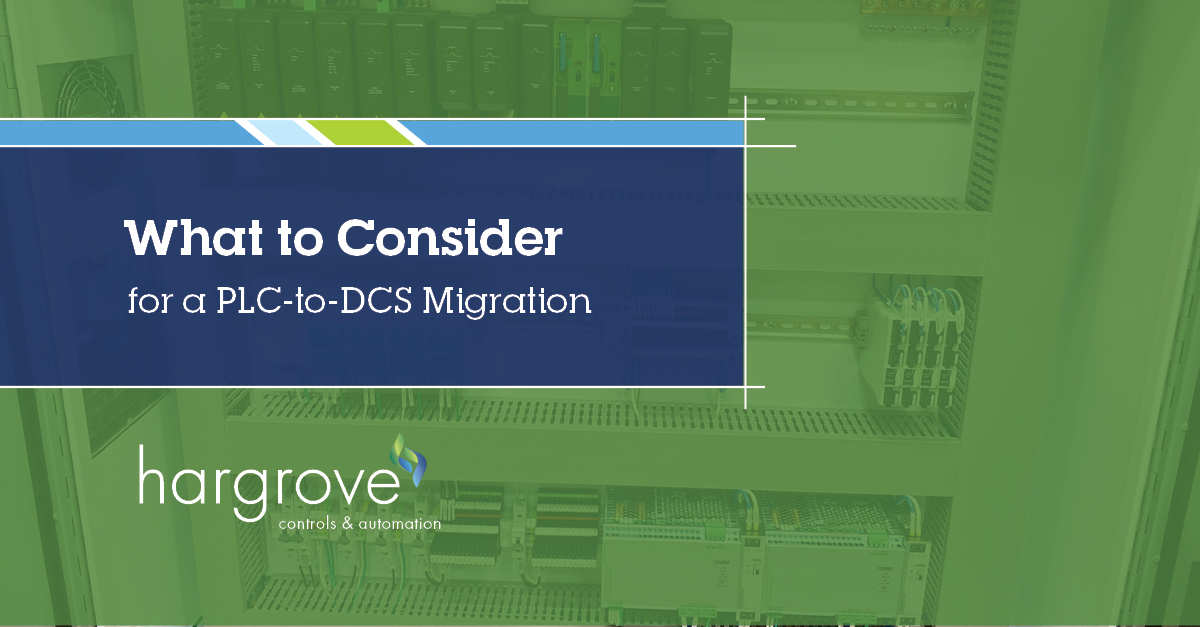
Migrating from a PLC system to a DCS is not an easy or inexpensive undertaking, so it’s important to understand the differences and know if it’s the right solution for your facility.
The Difference Between a PLC System and a DCS
A programmable logic controller (PLC) is an industrial microprocessor used for automation. PLCs are usually preferred for high-speed processes because they originate from more machine-oriented tasks. A distributed control system (DCS) is a control system for a facility used in continuous and batch processes. A DCS has a centralized database that performs a variety of tasks such as providing the controller data to operations, managing batches, or providing interconnectivity between controllers and I/O. A DCS becomes a ‘one-stop shop’ for the thousands of I/O points that you have in your plant. A DCS is a good choice when looking at complex operations, like a multi-step batch process or a facility that needs to produce a consistent product within a 2% margin of error and need niche batch software.
In terms of modern capabilities, there aren’t many differences between a PLC system and a DCS. Many modern PLC vendors sell software packages that can interlink PLCs and behave similar to a DCS. The biggest difference is how each is designed and what they’re intended to handle. PLCs tend to be standalone controllers, used for things like skid equipment. PLCs are more common in small plant operations, where you have fewer than one or two hundred I/O points. Whereas a DCS is more typical in a larger plant with thousands of I/O points or at a plant with more complex operations.
When to Consider Migrating to a DCS
In general, you should consider migrating to a DCS when the system has expanded to a certain number of I/O points, which depends on how large and complicated your process is. Another reason plants migrate to a DCS is because their PLC system is approaching its end of life and needs to be upgraded. As a system gets older and the employees who understand and maintain those systems retire, a DCS migration begins to make more sense.
A DCS migration is a large undertaking that is completed in phases. Because of the operational impacts, it can be an expensive and intensive project.
What are the Benefits of a DCS migration?
A DCS provides modern controllability—all the ‘bells and whistles’. A DCS can help you take a multi-variable process and see the exact conditions needed to generate a batch with lower and lower margins of error. With a modern DCS, the technology advantages provided with digital transformation give you more options. For example, you can experiment with simulations of your process, gather more accurate data that reflects your target key performance indicators, have versatile control schemes, and more.
Complications to Avoid in a DCS Migration
The complexity may make it tempting to put off a migration until the last possible moment. However, if you wait to start the project until your first system is failing, you will inevitably face downtime issues. A planned migration can take months, or even years. It’s a good idea to build a migration plan based on your system’s expected lifecycle; this way you can have the right personnel and spare parts on hand.
Two Approaches to a DCS Migration
There are essentially two approaches that you can take with a DCS migration. One approach is to look at the plant like it’s a brand-new facility. This involves reviewing the P&IDs and writing up new control narratives around how the facility will function and then programming the system based on that narrative. The system is programmed like it’s new, even if there is existing equipment or I/O. This is a good approach because it allows engineers to consider modern and best practices when designing the system, introducing extra efficiencies that may not have been available in an older system, and taking advantages of modern DCS capabilities.
The other approach is to reverse engineer the old system and duplicate it. This option can save time because you’re basically copying old code. However, this means you’ll have essentially what you had before. You’ll gain modern hardware and software, but much like putting an old engine in a new car, your system performance will be underwhelming. You won’t reap the benefits of a new and modern system, and it may be tricky to support. You gain DCS I/O capacity and a central database, but you may also inherit obsolete code.
Taking on a PLC-to-DCS Migration
A DCS migration is a significant investment, but it will prime your facility to be able to handle great complexity and a large number of I/O points. A DCS will also open new doors for modern advancements and technology benefits. It can also be helpful to engage support, such as that of Hargrove Controls & Automation.
If you’re considering a DCS migration, our Team can help you assess your current situation and address next steps for your migration. Contact us today.