Top 5 Benefits of Working with a System Integrator
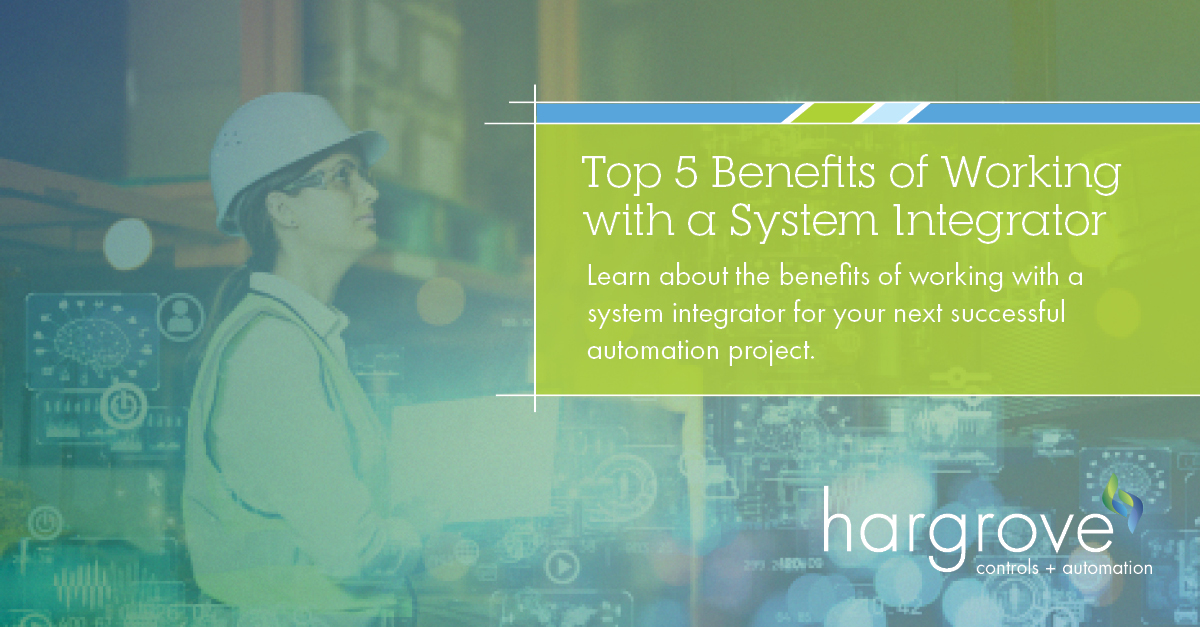
All manufacturing plant managers have projects that are multi-faceted. For example, a project may include flashing hardware, connecting servers, and upgrading software. Three separate jobs; three separate specialists all part of the same scope.
When hiring for your next project, you have several options: an original equipment manufacturer (OEM), a system integrator, or a small one-man operation. Your decision will depend on several factors. However, it’s helpful to keep in mind these benefits of working with a system integrator for your next successful automation project.
1. Well Versed in Multiple Platforms
Most sites consist of third-party equipment. For example, the OEM for a plant’s distributed control system (DCS) may be Emerson DeltaV, but that same site may have another OEM for historians such as Aspen IP.21 or OSI PI and PLCs such as Rockwell Automation, and a different system for machine monitoring protection such as Bently Nevada.
A system integrator has subject matter specialists (SMSs) in a wide variety of OEM products and technology at a particular site. With vast experience in multiple software and hardware systems along with process safety and further safety experience, they are able to integrate third-party systems using innovative and unique solutions.
System integrators understand communication protocols, so all systems can talk to one another and transmit data correctly. This includes understanding how to connect system to system, how to configure protocols within each system, and the ability to test control and communication to prove interfaces before on-site installation. Not only does this reduce downtime and increase productivity, but also provides cost savings.
2. Focused on the Bigger Picture
System integrators are not solely focused on the programming aspects of your project. They understand the overall process, from conceptualization to installation, and what makes sense for your plant. They are capable of simplifying projects by working with the engineering and execution team throughout the project lifecycle.
Using a system integrator with an EPC firm gives you the benefit of a full engineering team, including process solutions for plants. This type of system integrator can complete upfront engineering all the way through detailed design without the need to contract out engineering knowledge, enabling them to provide long-term solutions. This partnership also lessens the burden on the facilities managers who can focus on day-to-day production activities instead of coordination with multiple parties.
With built-in instrument and electrical personnel, system integrators bridge the gap in communication, creating a handshake that connects configuration, construction, and design. Since system integrators offer the I&E package, they take full ownership of the project, ensuring quality from start to finish. They focus on the right solution for each application regardless of the product line or vendor, so you only get what you need.
3. Offering Local Support
Most system integrators have the capability to provide local support with knowledge of local supply chain constraints. Proximity means they can also support in emergency situations and offer local factory acceptance tests. With local resources, the engineers they put on-site to commission systems are often the same engineers who will come back to maintain that system years down the road. With the same resource for each engagement, you can be sure it is someone who knows your facilities and processes.
Integrators are relationship driven. They don’t want to just complete a project; they want to continue that relationship by providing ongoing support to alleviate labor shortages for manufacturing leaders. There is also no requirement for full time support, allowing you the flexibility to staff your site on an as-needed basis.
4. One Point of Contact
A good integrator understands that communication is key to a successful project and has the personnel to manage a multi-platform system.
Instead of having to contact multiple people based on areas of competence, with a system integrator, it takes one phone call to reach an engineer that can promptly answer your question or respond to your problem. One contact from your system integrator can assist with software applications, hardware, process, controls, batch, and is familiar with not just the configuration, but with the servers, infrastructure, and switches.
5. Providing Customized Solutions
Since system integrators are well versed in multiple platforms, they are flexible and able to provide customized solutions in integration and panel fabrication. They understand the products and are able to borrow hybrid pieces of equipment to make modifications for system functionality, circumventing some of the current automation supply chain issues plaguing the manufacturing industry.
System integrators are not selling specific hardware from a particular vendor but are responsive to your needs and what is best for your project.
Teaming with Hargrove as your System Integrator
From appointing local personnel who are well versed in multiple platforms to providing customized solutions, system integrators have the knowledge and flexibility to assist you based on your specific needs.
As a relationship-based and vendor-agnostic system integrator, Hargrove Controls & Automation creates robust automation solutions that drive results for clients. With panel customization capabilities, Hargrove has a deep bench of process control specialists and local offices across the U.S. to help you with your next automation project.
To Team with Hargrove, visit our website.