Three Keys to Conducting a Quality Process Hazard Analysis
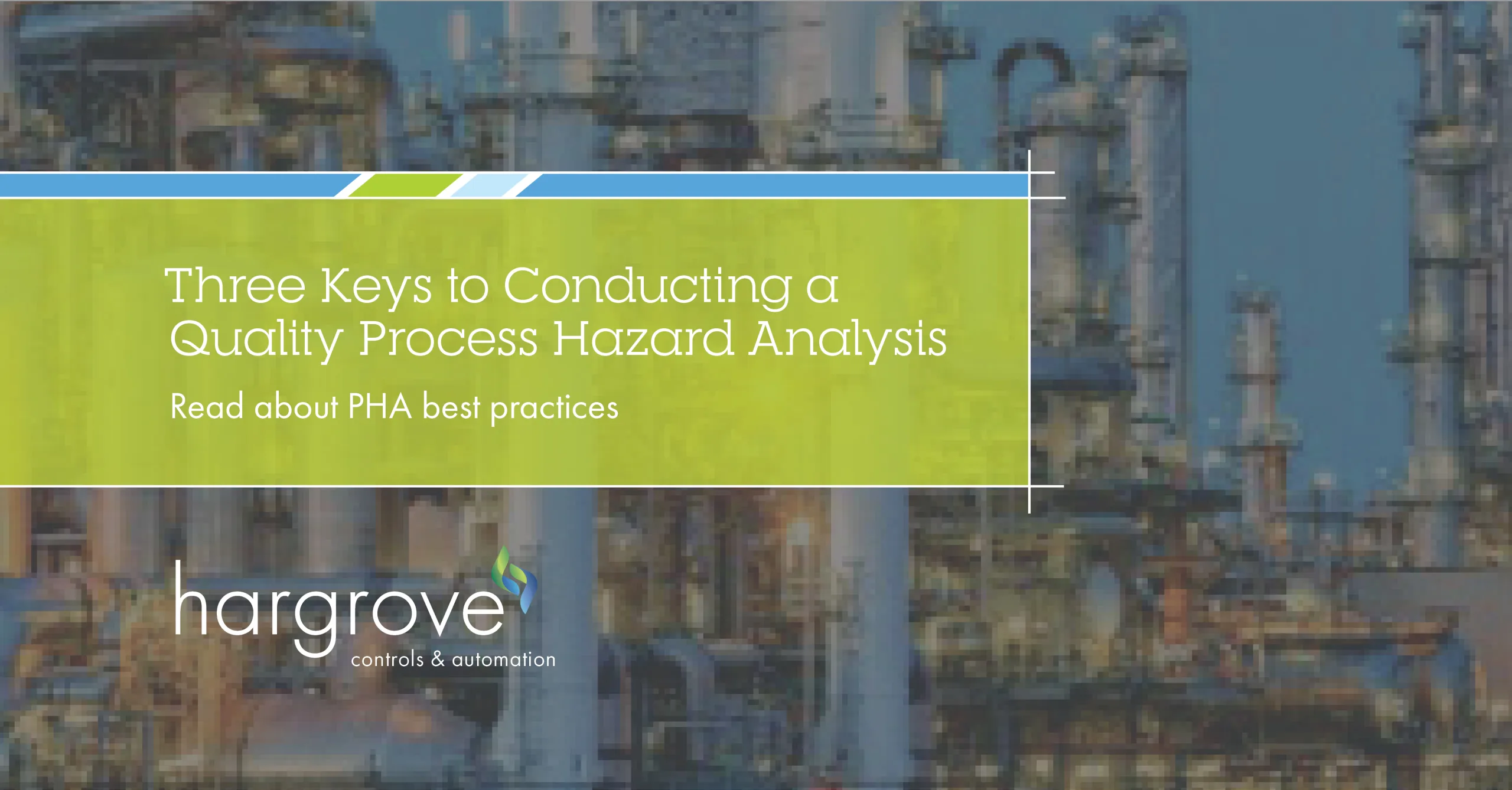
A process hazard analysis (PHA), also called a risk analysis for hazardous processes, is a systematic examination of a chemical or manufacturing facility to document the hazards inherent in the specific processes used there. It analyzes the different ways a process can deviate from what it’s supposed to do and examines what safety, environmental, or business risks can come as a result.
PHAs are required by the Occupational Health and Safety Administration (OSHA) to protect workers and the environment from any industrial process that uses hazardous chemicals, such as those in the petrochemical, specialty chemical or refining process industries. During the design of a new facility, PHAs are conducted to ensure the process risks can be properly mitigated and to make sure the design is safe. It’s more costly to implement safeguards late in the design phase rather than earlier on in the conceptual, basic, and detailed engineering phases.
A PHA can take from a few days up to several months depending on the complexity of the process being inspected. Here are a few keys to conducting a quality process hazard analysis.
Quality PHA Key #1: The Right Team
Putting the right team together is an essential element for a successful PHA. The size of the team and key roles to be filled for a PHA will vary depending on the site and complexity of the process.
The facilitator’s role is to plan, facilitate and manage the PHA, and is often required to be from outside the plant’s organization. An outside facilitator has less skin in the game, so they’re able to look at the process with fresh eyes and not have some of those biases that can crop up when you see the same thing all day, every day.
In addition to the facilitator, the scribe position is also required. The scribe plays the vital role of accurately and completely recording the significant discussions and results of the PHA.
A process lead is another critical PHA role – someone who’s very familiar with the chemistry of what’s happening. Additional roles needed are controls and mechanical specialists. You might need to know design parameters for certain equipment, pump information, or details about rotating machinery.
For facilities that have been running for several years (not in design-phase PHAs), it’s important to have operators involved in the PHA. They can help identify discrepancies between the facility’s design and how it operates in practice. They can also discuss the actuality of operations, which will likely help uncover process safety risks that weren’t considered in the design.
Many of these roles aren’t strictly exclusive, meaning you don’t have to have a different person for each if someone has multiple applicable skillsets. There may not be a separate scribe on a PHA since the facilitator can act as scribe.
Depending on the process, the PHA team could be two or three people, or more than a dozen. It doesn’t necessarily matter how many people are involved. It matters to have the right people. Ensure that your team is composed of the people who have applicable knowledge to the process and who can cover a lot of topics such as the specific rules of the PHA.
The right team starts with a good knowledge base and getting the right people involved.
Knowledge Base and Roles for the PHA Team
- Facilitator
- Scribe
- Process
- Operations
- Controls
- Relevant mechanical knowledge
- Operator experience
- Rules of the PHA
Quality PHA Key #2: A Clear and Consistent Set of Rules
To maintain consistency throughout not only a single PHA, but across a facility, a clear and consistent rule set is required. Clear and consistent rules help you avoid problems such as applying rules unequally to different sections of a plant or applying the same rule in different ways to a certain unit. Inconsistency can lead to gaps in the PHA which could be a safety risk.
Typically, the PHA rules are given to the team at the start of the project and are based on international standards and recognized engineering practices.
Everyone has a different level of acceptable risk, so you must adjust your facilitation accordingly. Additionally, some facilities will take credit for certain types of installed safeguards – check valves, for example – and other places will not take credit for these devices. A clear and consistent set of rules will create uniformity among the different locations.
A clear set of rules is also helpful when the PHA team has members rotating in and out. In a lengthy PHA, not everyone may be able to stay on the team for an entire month at a time, making it necessary to swap out team members. Applying the rules the same way throughout ensures a consistent product throughout the entire site.
Quality PHA Key #3: Good Documentation
The final key to a successful PHA is creating good documentation. Keep in mind that the document must be robust enough to answer questions for future PHA teams as well as those implementing current recommendations.
Whoever is documenting the PHA must remember that the current PHA team is not the only group to ever read that PHA. Other teams will also be using the PHA to design safeguards to mitigate the identified areas of concern throughout the facility and determine independent protection layers (IPLs).
Many people will use the outputs of the PHA for their work who may not be familiar with the context of the PHA, so it must be able to stand alone. That means clearly documenting assumptions and ensuring that the consequence descriptions are correct.
This is especially important because the document will be used five years later for revalidation. The consequence needs to be fully described to adequately determine the safeguards.
The goal is to be able to have someone look at the PHA documentation after the team has disbanded and understand exactly what was discussed.
Working with Industry Specialists
Hargrove Controls & Automation’s seasoned and highly-trained Process Safety Team helps clients operate safe facilities and comply with OSHA process safety regulations.
With a combined 85+ years of process safety experience and having conducted dozens of PHAs, our engineering staff has conducted PHAs and revalidations for a wide range of processes and knows how to efficiently and successfully facilitate these projects.
For more information on Hargrove Controls & Automation’s process hazard analysis services, visit our website. Let us guide you to a safer facility. Contact us today.