Strategies to Navigate Automation Projects During Supply Chain Challenges
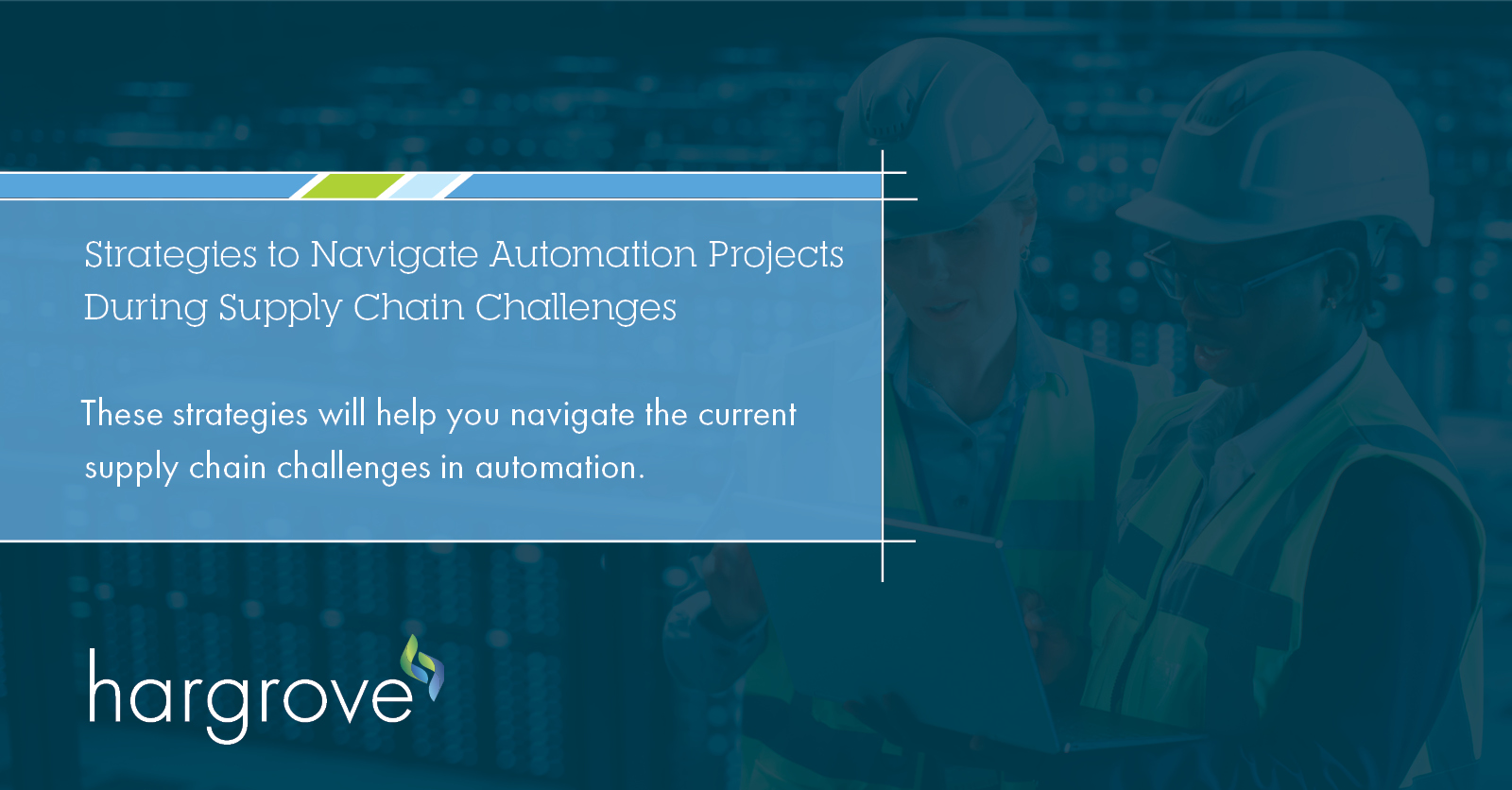
Imagine building your dream home. You spent the past year choosing a contractor, designing the floor plan, and picking out the paint, carpet, and trim. The contractor is working hard to remain on schedule so you can host your first Thanksgiving meal. Eager to see the progress, you plan a site visit. As you pull up, you notice the front door and windows are still missing. Before you put the car in park, the contractor approaches your car, apologizing and informing you of a three-week delay.
The current state of the supply chain has become a huge obstacle for every industry including manufacturers looking to implement automation plans. With part-sourcing issues and back up lists running dry, there is no shortage of challenges for the engineers and managers who must keep projects moving.
Often, falling behind schedule or shutting down isn’t an option. Here are a few strategies that will help you navigate the current supply chain challenges in automation.
Getting Creative with the Supply Chain: the ‘Frankenstein’ Approach
Standardization is the key to success, especially when you are trying to run a lean business. However, in today’s environment, that approach may not allow for the completion of projects that increase the capacity of your plant or the launch of new products. At the end of the day, what matters most are the key drivers of success to your business. The means to achieve those drivers can be adapted and modified to best fit your business.
When standardization stands in the way of moving a project forward, engineers must get creative. Some teams choose to build a ‘Frankenstein’ system, where engineers take an available PLC from one distributor, an available HMI from another, and add the remaining parts from whichever vendor has them in stock. For example, one vendor may have an abundance of controllers and be lacking in input/output cards. Another supplier may have an abundance of I/O cards, but they are struggling to supply controllers.
By removing the typical one-brand restriction, system integrators can source available alternative parts to cut down on extraordinarily long lead times. In cases like this, it’s important to consider a system integrator who has the right Team to seamlessly integrate the equipment into a cohesive system and can offer support your future maintenance needs.
“We’ve got a deep bench. We excel because we have someone who is great with every brand of system that we service,” said Daniel Shaw, Discrete Manufacturing Industry Leader at Hargrove. “We call in our subject matter experts as part of each project. Since Hargrove is brand agnostic, we utilize our knowledge across a multitude of OEM control systems and components and apply that deep domain experience to make our projects successful.”
With the ‘Frankenstein’ approach, there is no one size fits all, but it helps to avoid certain pitfalls. This tailored, case-by-case approach allows for more flexibility to ease those staggering lead times and get equipment installed more quickly.
“The quality of the system integrator you choose to create a ‘Frankenstein’ system is important. You really need to consider who you’re using, what their credentials are, and how they can support that equipment,” said Shaw. “At Hargrove, we are able to support a wide variety of brands.”
Upfront Engineering Studies Can Offer Big Savings Down the Line
Ultimately, the best way to tackle supply chain issues is on the front end. Instead of putting already busy plant personnel on this task, partner with a system integrator to budget for an engineering study. Allow an experienced system integrator to spend a few weeks researching the existing system and new project scope to determine what is available and what makes most sense for your solution before quoting the larger automation project.
An engineering study allows the subject matter expert to make a reasonable assessment of what equipment is needed and to figure out how to bridge the gap if one exists. The system integrator should have close ties to the market and years of experience solving this type of problem.
“If you send someone in from the plant environment that doesn’t put systems together every day, they’re at a disadvantage and they may not even know they’re at a disadvantage,” said Shaw. “Without upfront research, the automation project may go down a path that is not feasible due to design gaps or unanticipated supply chain delays. Problems like this are typically uncovered right before installation when project recovery costs triple.”
In addition, engineering studies help to prepare better for the potential for further shifting dates in the supply chain. The fully funded project could be ready for installation but missing just one part. That one part could push the finish date back months, with the project sitting idle. With a strong plan in place at the start, the system integrator can have more flexibility to schedule around possible issues.
Working with the Right System Integrator
Automation is facing many ongoing difficulties due to supply chain constraints. However, by teaming with the right system integrator, you can develop an engineering study and a solid plan to ease supply chain pain points.
To learn more about how Hargrove Controls & Automation can work with your Team to tailor a solution for you, contact us.