Chet Barton Discusses Process Safety in Control Global Articles
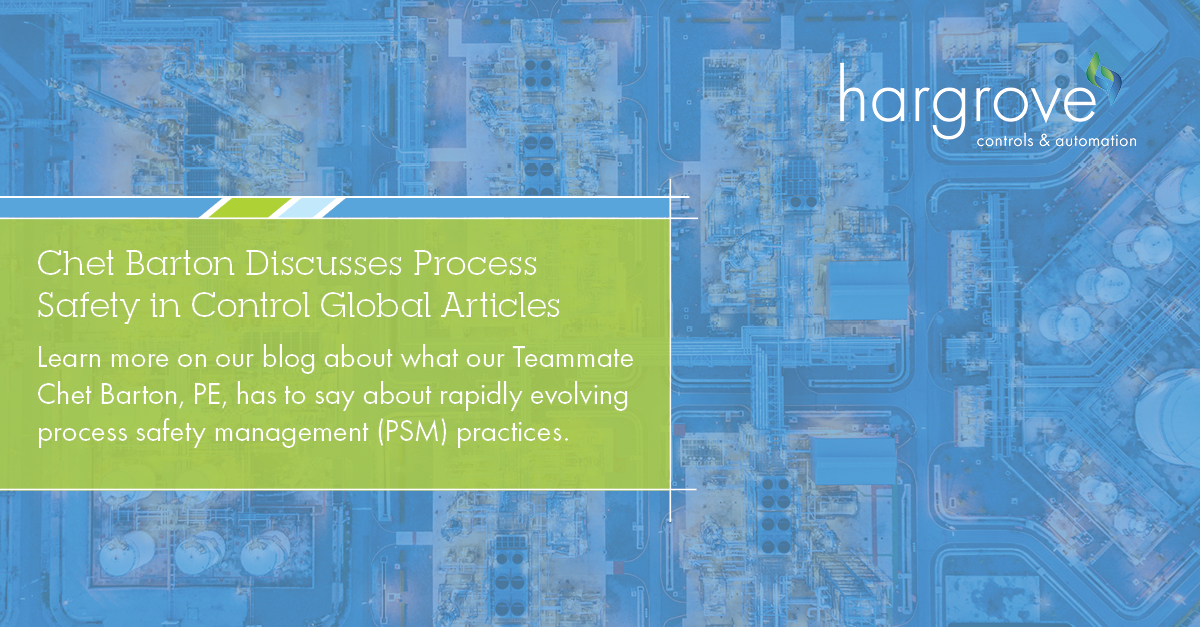
Chet Barton, P.E., F.S.Eng., a controls and automation process safety industry lead at Hargrove Controls & Automation, joined Control Global, a magazine exclusively dedicated to the global process automation market, to contribute to two process safety articles written by Executive Editor Jim Montague.
Read the original articles by Executive Editor Jim Montague entitled, “Process safety boosted by digitalized lifeline” and “Linking safety disciplines, professions and training” on the Control Global website.
Process safety requires enhanced awareness, effort, and discipline and has never been considered easy, but it is becoming less difficult due to the digital transformation and present-day improved software. Barton attributes this development to the recent COVID-19 pandemic, which drove companies to perform process hazard analyses (PHAs), layers of protections analyses (LOPA), and other safety tasks online by their newly-formed work-from-home employees. “It used to be rare to conduct a virtual PHA, but priorities shifted during the pandemic. While it once seemed critical to have everyone in the same room, some clients began prioritizing project schedules over the in-person experience,” says Barton. “We set up Teams meetings, share our screens, look at the P&ID and other PHA documents, and pretend we’re there in person. Everyone was worried initially because we always met in-person before, but we learned that we could do the PHA remotely because its essence is just a discussion about what hazards could be there and what to do about them.”
Barton continues, “Since we’re mainly talking about hazards, consequences and mitigations, it’s possible to do a remote PHA by practicing some of the basic work-at-home skills. Many users and companies are realizing that remote work is OK, and the same is true for doing PHAs. Once you try it and get used to it, it works.”
“This is similar to what happened with predictive maintenance and advanced process control (APC), which have been available for a long time and got more sophisticated, but can generate so much data that users don’t know what to do with it,” says Barton. “We work with many users that don’t have the time to input and keep up with safety data because they’re mostly worried about keeping their processes up and running.”
Barton believes remote work and digitalization will have big impacts on process safety and encourages streamlining the data that safety protocols rely on for easier accessibility. Making this data more transparent can save time and effort and increase the chance of success for safety procedures. “The problem is that many clients who want to improve process safety have a hodgepodge of systems and safety documentation, which is often outdated or lost, and this stops their safety programs from getting started,” says Barton. “That’s why some hire us to perform audits, fill in gaps in their safety programs, and update existing documents or generate new ones. These documents include PHAs and LOPAs that are supposed to be revalidated every five years. They also include safety interlocks based on the PHAs and LOPAs that address specific operations, safety scenarios and mitigations, which should also be tested periodically.”
Barton says, “Unfortunately, there are many times when this hasn’t been done for a while, so users must make lists and check the accuracy of the ones they can find, produce new interlocks for each one that can’t be found, and develop safety requirement specifications that define what each interlock should do. Each facility typically has hundreds of interlocks. Usually, we can find documents for half of them, and half of those are usually correct. Luckily, software is getting better at organizing all this data, and this can help process safety, too.”
Barton went on to say that there are specific tools that consolidate all safety data in one centralized place for easier access and documentation. Hargrove works with clients of various sizes and advancements, including clients that have no previous procedure for testing its interlocks. With no procedure in place, there is no way to know if the system is working properly or if protection would be provided if/when an event were to happen. “Any type of process application can lack effective interlocks and testing, so we help users update or generate them, write procedures, and train staff to do periodic testing,” says Barton. “Just like with diet and exercise, if they do what’s right, then there’s less chance of safety issues and incidents, and the whole process application is healthier and has a higher general safety level. And everyone can take satisfaction from it because they’re not only protecting their people but also the surrounding community.”
Training is also vital to the outcome of the safety systems, a service that Hargrove offers its clients. There are multiple things you must get right in order to meet the requirements of Process Safety Management (PSM) from OSHA and the process can be very daunting. “More and more clients are asking for training programs from our process safety group,” says Barton. “Standards like IEC 61511 call for facilities to train operations and maintenance staff in process safety, so there’s an understanding of interlocks and how to respond to alarms quickly. An increasing number of refineries and chemical manufacturers are seeking more formal instruction on safety interlocks and protective layers.”
Hargrove Controls & Automation was named System Integrator of the Year 2022 by Control Engineering/Plant Engineering magazine and is a certified member of the Control System Integrators Association (CSIA). For more information on process safety services, please contact us.