Reliability, Availability and Maintainability (RAM) Modeling: A Proactive Approach to System Performance
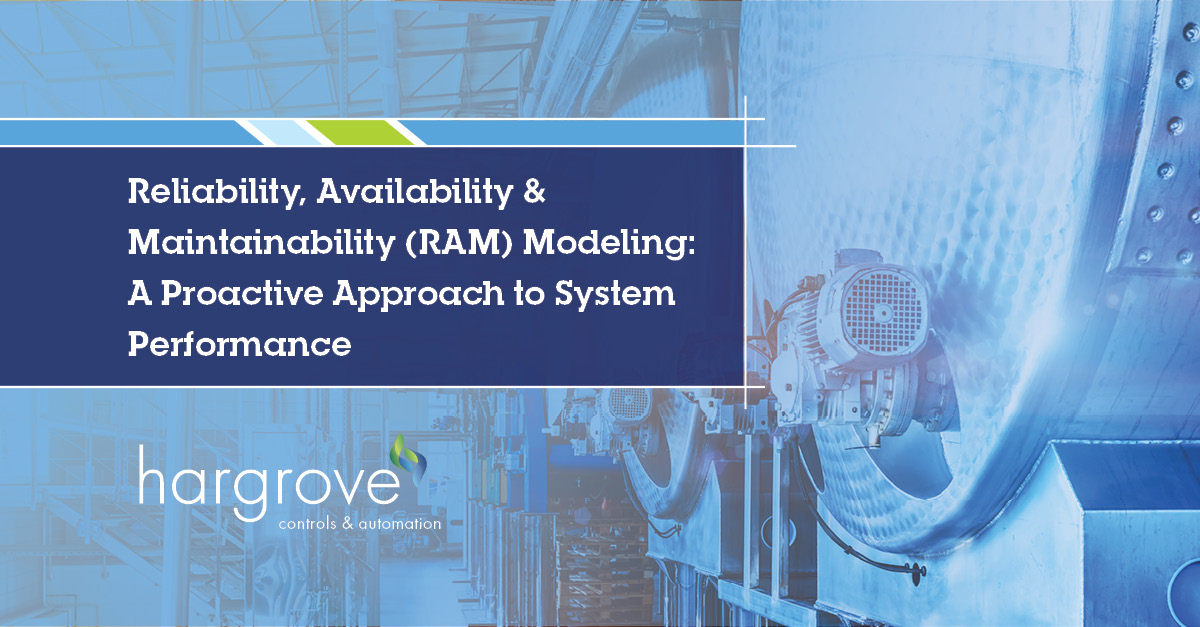
By Matthew Buker, Controls & Automation Digitalization Specialist
Weather forecasting uses quantitative data to predict future weather conditions, allowing the public to be warned in advance of potential threats to their geographic location. Forecasts can also be used by agricultural companies to make daily decisions about their crops, utility companies to estimate future demand, and everyday people to plan their day.
At a manufacturing facility, the ability to predict future conditions can empower your personnel to make informed decisions about operations, resulting in reduced unplanned downtime and lower maintenance costs. Reliability, availability, and maintainability (RAM) modeling provides insight into existing process design, plant equipment, operations methods, and maintenance plans.
Understanding RAM Modeling
A variety of advanced control solutions, including model-predictive control (MPC) and fuzzy neural networks, analyze current conditions to optimize an output. However, these solutions are limited to adjusting one or more manipulated variables and can’t analyze the process design. They also only apply to plants that are already built and running.
RAM modeling is a methodology that captures real-world behavior of all components in a process to determine their statistical reliability. The probability of failure for each component is entered into an algorithm to determine the total probability of failure for the process. RAM modeling inputs can include outside and environmental variables that are not part of your process, such as planned downtime, maintenance variables, the probability of your utilities going out, or the probability of a storm to determine how throughput is affected. RAM modeling can also be performed on both running plants and at the design stage.
A Breakdown of RAM Modeling:
- Reliability: Probability of failure over a predetermined time interval
- Availability: Percentage of expected uptime
- Maintainability: Frequency of system maintenance
RAM modeling is a technique that inputs potential variables and analyzes a system’s capabilities, identifies potential causes of losses, and quantifies the reliability of plant equipment to establish expected uptime of an entire production unit or site. RAM modeling performs Monte Carlo simulations of the plant lifecycle, simulating different versions of potential outcomes to determine the odds of various combinations of failure and availability patterns that predict your plant’s uptime. It’s a level of design verification beyond the classic mass and heat-flow calculations or reaction-kinetics predictions.
Applications of RAM Modeling
Design
Overcoming design deficiencies can be costly and might not provide optimal solutions. RAM Modeling questions your process’s design, considering alternative solutions and providing insight into the optimal choice.
Any manufacturing company looking to design a new plant can use RAM modeling by determining the probability of failures at their current plants to predict the future plant’s reliability. Suppose you are starting from scratch without an existing plant. In that case, you can input industry handbook data and insights from engineers to simulate different versions of a process using different equipment and process controls and compare their reliability and availability.
RAM models can be a valuable design tool to make sure buffer tanks are sized properly or parallel equipment is included where needed.
Efficiency
While traditionally used in the design phase, RAM modeling is beneficial for any industry where downtime is critical. It can help existing plants identify issues within a process, determine if a system was optimally engineered, and ultimately increase efficiency from their processes. If your site is experiencing unplanned downtime and not meeting its theoretical maximum availability, RAM modeling answers the question, “Why?” It identifies the cause of failure and determines which components contribute the most to failure and which should be upgraded.
RAM Modeling helps operators make informed decisions and improve operational strategies. For example, it can provide insight into programming and managing process controls. If a buffer tank is nearing capacity, is it better to run at full rates and stop at the high-level limit or reduce rates to buy more time? It can also help to determine or adjust maintenance schedules, assess spare parts inventory, and evaluate raw material supply plans.
Conducting a RAM Study
A RAM model study involves a multi-discipline, system-level analysis of a production area. Input from process design, production, operations, maintenance, and process control is essential to gather insights into the system’s current operating status compared to its design. However, most studies are completed in just a few weeks.
Improving System Performance at Your Facility
Whether you are designing a new plant or improving efficiencies in an existing plant, RAM modeling can provide you with applicable information to make informed decisions about operational and maintenance strategies. Our industry specialists can help. Contact us today.