Tracking Key Performance Indicators (KPIs) in the Pulp & Paper Industry
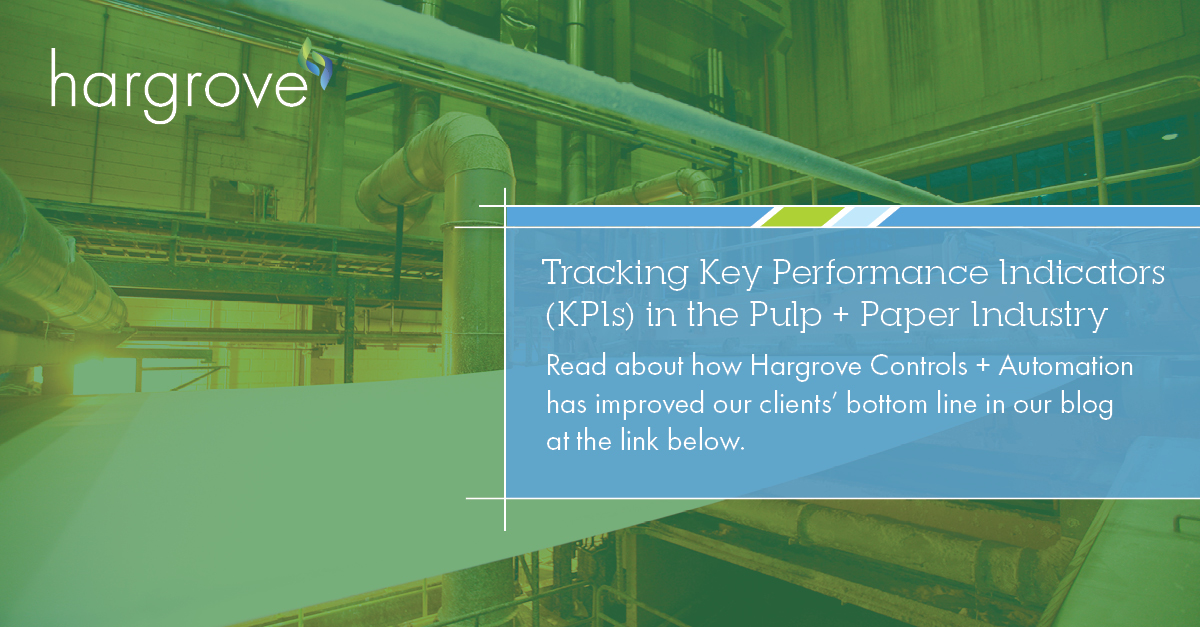
KPIs in the Pulp & Paper Industry
Key Performance Indicators, or KPIs, are data points that can be easily tracked and carefully chosen to align with your business goals. Data collection is most effective when it is properly tracked and conveyed in a meaningful way. By aligning data points with KPIs, a bigger picture will form. When starting with KPIs, it is best to start with just a few, which will allow you to focus on what will make your business more successful. Other KPIs can be added later on as needed.
In the pulp & paper industry certain product lines can have a very low margin. This makes tracking KPIs crucial to maximizing site asset performance. These are the most common KPIs that Hargrove has seen in this industry:
- Cycle Time
- Equipment Uptime
- Throughput
- Asset Capacity
- Production Cost
- Production Waste/Defects
- Demand Forecasting
- Return on Assets/Return on Investment (ROA/ROI)
- Customer Complaints
- On-Time Delivery
KPIs also provide insight into your team’s manufacturing process and help you to make more informed decisions. In the pulp and paper industry, a lot of facilities focus on lean manufacturing and eliminating wasted product, time, and labor. By tracking things like throughput, production waste, and cycle time, you can find innovative ways to optimize your production. Here are some examples of areas of improvement our clients at Hargrove have found by teaming with us to review their KPIs.
Product Output Demand
While reviewing the KPIs, one client found that their throughput and sales demand were not matching up. Production was already running at full throughput, but they needed a way to meet the high demands.
The main issue was with their consumer product lines. By reviewing KPIs with our Team, they came to a solution: reducing the width of each paper roll by 1/8th of an inch. By making this adjustment, the client would be able to produce one more roll per cycle. This allowed production to run over capacity with only minimal changes. With the success of the initial lines, the client pushed this to other product lines as well.
Grade Change Waste
Another client needed to increase production of coated boxes but needed an innovative solution to improve their equipment uptime.
By reviewing KPIs, it was found that this client was producing a lot of waste during grade changes. The grade change was taking upwards of an hour from the wet end to the dry end. The team was able to modify the procedures and get the grade changes down to 10 minutes. This added back 6 hours of production per month for the client.
High Production Cost
A client was struggling with increasing their overall bottom line. Their KPIs were showing that they had a high production cost, and they began looking for ways to run more efficiently.
In this process, they found that their city water bill was relatively high. The team installed temperature sensors on turbines and other water consumers. Once the optimal temperatures were found for each stage of the process, the system could maintain that temperature with less freshwater, which then reduced the amount of water being used, thus reducing the cost of water and improving their bottom line.
Conclusion
Our Subject Matter Specialists (SMSs) have decades of experience working hands-on roles in pulp & paper and have developed industry-specific ways to track KPIs. To begin your journey with KPIs and make your site more efficient, contact our Team today.