Using Artificial Intelligence to Improve Plant Reliability, Efficiency, and Profitability
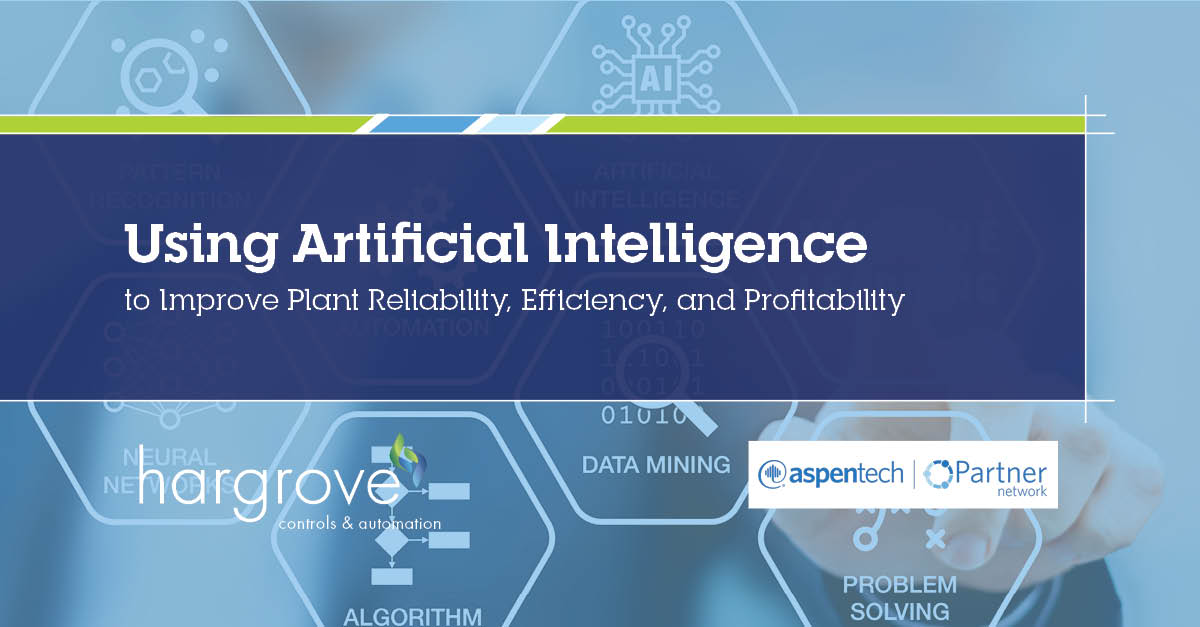
New AI technologies enhance your automation systems, expand your manufacturing capacity, and optimize your productivity. So why are so many plants struggling to gain traction with implementing these new technologies? Perhaps there are so many options on the table you find it difficult to sort through the various types of products available. It can be difficult to determine the best starting point to realize the greatest return on investment that will catapult your plant into more opportunities.
Or perhaps you’ve seen a demo of a new software package, but realizing the time, effort, and cost necessary to implement it effectively at your plant, you’ve been discouraged. Maybe it’s because the idea of adopting Industry 4.0 seems daunting when you know your plant hasn’t yet fully adopted Industry 3.0 best practices. Our experience tells us that implementing even two or three Industry 4.0 initiatives can provide substantial benefits, even though the idea of full Industry 4.0 implementation may seem out of reach. It can be much like eating an elephant… it’s best one bite at a time (or is it byte in this case?).
Hargrove has experience on a multitude of AI technologies currently available in the marketplace. We help our clients identify the best options to get started or to continue their digitalization journey. Some of our greatest success has been with our partner AspenTech. This partnership helps ensure our team is highly skilled on all of AspenTech’s product offerings, and we stay on the leading edge of their technology updates. Below are some of the products with which we’ve had our greatest success, any of which could serve as your starting point.
Predicting Equipment Failure with Aspen Mtell®
Unscheduled downtime can be catastrophic for your bottom line. When your equipment shuts down, your revenue stops. Even where you may be able to continue production in some capacity, a bottleneck that halts output on one or more of your largest revenue drivers can be devastating.
Historically, control systems engineers have only measured a limited set of potential indicators of equipment failure, such as discharge pressure, vibration, temperature, or power draw. Because of this, predicting equipment failures has only happened with limited accuracy and typically only after damage has already occurred. While multiple data points can be leveraged to create more accurate predictions of possible machine and equipment failure, facilities were still faced with short notice about potential issues.
The AI-powered Mtell leverages multiple data points to create models that are used to detect and predict future anomalies and failures weeks and months in advance. Mtell uses maintenance data, historical process data, and current process data to identify and predict future equipment failures before any damage has ever occurred. Over the first few weeks post-deployment, Mtell’s low-touch machine learning improves its pattern recognition capabilities to more accurately distinguish between normal behaviors and anomalies. As it learns, the rate of false positives that commonly occur with model-based solutions decreases significantly.
Mtell doesn’t only tell you when your plant assets may fail. It provides you with prescriptive advice for preventative maintenance and remediation so that you can avoid equipment and machine failure before it happens. Moreover, Mtell’s monitoring and prescriptive maintenance capabilities are applicable across industrial sectors. Mtell has been successfully used in plants and production facilities in the following industrial sectors:
- Hydrocarbon processing
- Mining
- Petrochemical production
- Pharmaceutical manufacturing
- Pulp and paper production
- Transportation
MTell can be deployed in a fraction of the time usually required for site-wide or enterprise-scale rollouts because it typically requires no additional field instrumentation or hardware. Given its rapid rollout capacity, you can protect your production assets in no time, saving yourself excessive repair costs and production losses. Mtell is an excellent candidate for entry into new AI technologies due to ease of implementation and easily quantified returns.
Effective Planning for Future Expansion with Fidelis Reliability®
Preventive maintenance is far from the only practical application of the predictive power of AI. When you’re considering a capital improvement — whether greenfield or brownfield — you need to understand the full economic picture. You must account for your current performance and reliability measures to help project what equipment and plant resources your expansion requires. You must also accurately project how a newly integrated process will perform in conjunction with the existing facility before you finalize your design.
Furthermore, your projections should take into account production operation strategies as well as revenue. You need to verify how to operate your three parallel pumps, how to plan maintenance strategies for your exchangers, and how to manage raw materials deliveries at the design stage, not after the plant has begun to operate. Fidelis will help address all these challenges.
Fidelis allows you to generate a digital twin of your existing physical equipment and develop a model that incorporates typical process design information from applications like HYSYS or other process design tools with equipment reliability and availability information. Fidelis performs statistical simulations to integrate process physical constraints with “what if” scenarios to determine overall equipment effectiveness and plant performance. What sets Fidelis apart is its ability to model the cash flow of your production process, not just product flow. You can see how your entire product flow, down to each piece of equipment, adds to your bottom line and design your upgrade accordingly.
Fidelis Reliability’s robust modeling capabilities further allow you to integrate various real-world factors, such as weather-related shipping delays, equipment failures, warehouse spare strategies, and maintenance plans. Being able to generate models that cover a full range of operating variables helps you design your project in a manner that not only achieves nameplate capacity but also:
- Keeps operating expenses low
- Maximizes profit
- Avoids capital overspending
- Prevents the formation of new bottlenecks
- Predicts future performance of the overall system
We can get you up and running with Fidelis, with or without on-premise installation. Fidelis is a great tool to use on existing facilities, but it can be implemented with very little cost and effort when utilized as part of a capital project design effort, making it an excellent candidate as a starting point on your digitalization journey.
Enhancing Process Control with DMC3™ APC
While Advanced Process Control (APC) is commonly associated with distillation column control in the refining sector, the true potential of APC is much broader than one industry or process. An APC package like DMC3 aids engineers with continuous model optimization and rapid controller deployment to optimize production across the whole enterprise, as well as at the plant or unit level.
APC has been around for a while, but traditionally, APC software packages have been resource-intensive to use, requiring a full-time APC engineer (or several) to continuously maintain APC software. However, simplified workflows make DMC3 easier to use than older APC packages and simpler to roll out across your enterprise without the need for in-house APC experts. With AI-powered continuous self-maintenance, learning, testing, and optimization in real-time, DMC3 reduces energy consumption, increases throughput and yield, and, ultimately, maximizes profit.
You can monitor key performance indicators (KPIs) at the unit, plant, or enterprise-level through production dashboards. You can also coordinate multiple APC controllers to optimize planning, scheduling, and operation in real-time to reduce margin leakage. DMC3’s integrated platform is more agile, robust, and responsive than other APC packages. It can help you develop sustainable production improvements in any continuous industrial process sector. As an entry point into APC, it’s common to just pick one area of a facility or a particular piece of equipment to begin. Once you’ve been able to prove the returns, you’ll have the justification to continue the implementation effort.
These AI-powered technologies are just three of the options out there that can sustainably improve your production outcomes. If you are interested in the benefits that these or other AI-powered technologies can provide your plant or enterprise, contact us. We can help you learn more about these products and other related solutions.