Process Safety and Swiss Cheese
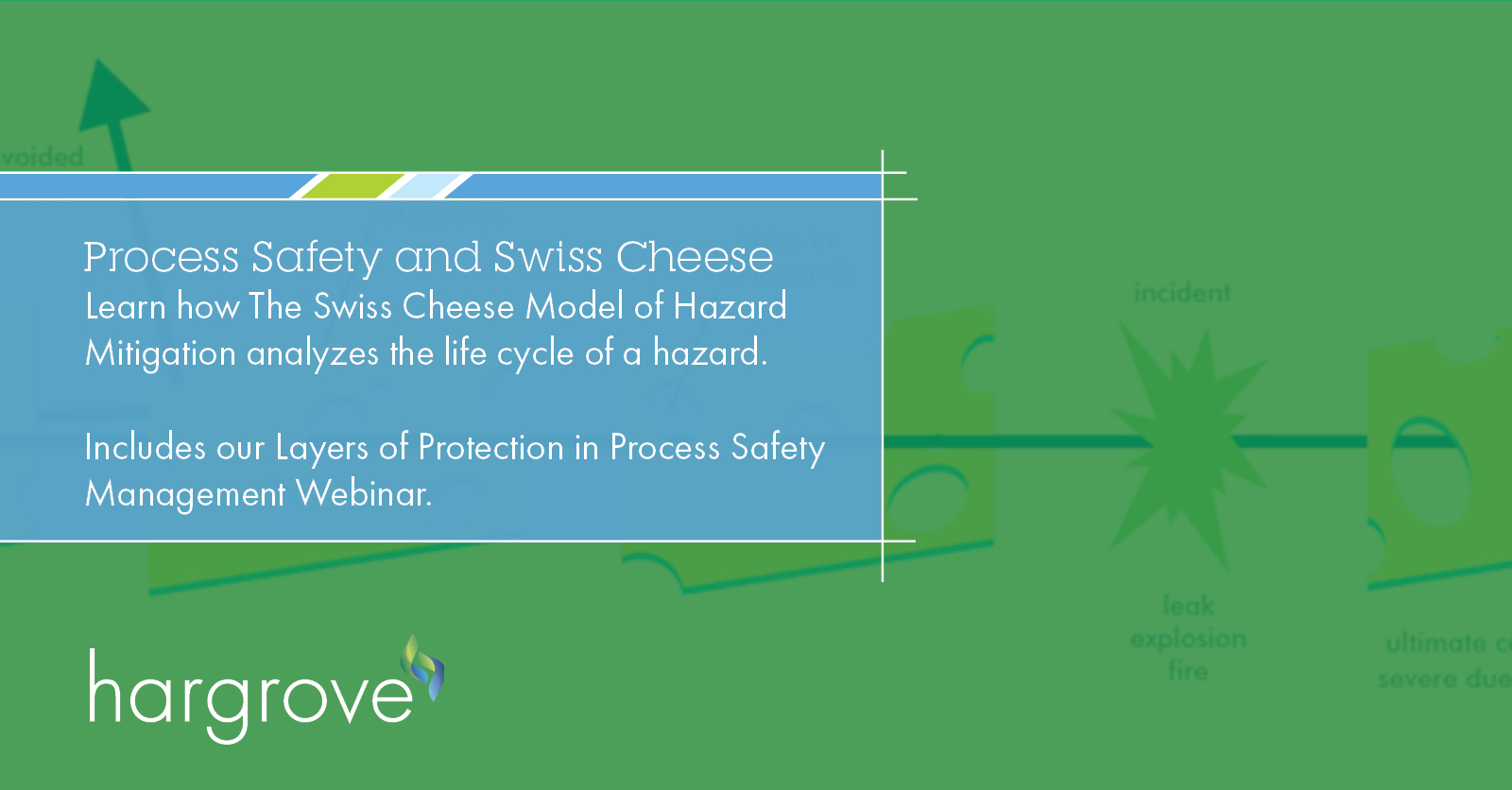
There is a certain amount of inherent risk in everything we do, even walking across the street. One is more likely to encounter an accident if they fail to look both ways and may be protected if they choose to mitigate risks by using several layers of protection, such as staying aware and utilizing crosswalks. One must consider the layers of risk, and the mitigation efforts they will use ahead of time in order to best approach a given activity. A given set of circumstances may be riskier than others, and therefore more likely to cause an accident.
Chemical processing facilities have similar inherent risks. If a hazard evolves, what safeguards are in place to prevent it from progressing to a severe incident? Are there mitigation efforts to consider? What if you could easily estimate the likelihood of an incident occurring and the severity of potential consequences?
The Swiss Cheese Model of Hazard Mitigation
The Swiss Cheese Model of Hazard Mitigation analyzes the life cycle of a hazard. The layers of Swiss cheese represent protective layers or safeguards which inhibit the hazard from evolving or minimize the consequences. The holes in the cheese represent weaknesses or failures in these safeguards. In some of these instances, the hazard is blocked from proceeding and will not evolve into an incident; however, in others, the hazard proceeds unhindered.
In our previous example of walking across the street, the safeguards would include things like crosswalks, walk signals, and looking both ways before proceeding.
For the safety and wellbeing of our workforce, government systems have enacted laws requiring certain measures to prevent or minimize catastrophic incidents. Therefore, every chemical processing facility must perform a process hazard analysis on their site.
In these analyses, the risk level associated with a hazard is compared to an acceptable level of risk to see what actions need to be taken. If the consequence is extremely unlikely or the severity of the consequence is small, it may be an acceptable level of risk. If not, this scenario should be analyzed further. A common quantitative method for further analysis is called a Layer of Protection Analysis (LOPA) where engineers delve into the details of the safeguards and protective layers. A LOPA quantifies the various safeguards as independent protection layers and allows the team to take certain credit against the risk of the Process Hazard Analysis (PHA) of that scenario. It is important to note that not all safeguards will qualify as Independent Layers of Protection (IPL).
What Qualifies as a Layer of Protection?
Join our host, Chet Barton, Hargrove’s Process Safety Group Leader, in an educational webinar, Layers of Protection in Process Safety Management, as he provides a thorough interpretation of the core attributes of an independent layer of protection, details what stakeholders in process industries such as refining, petrochemicals, chemicals, oil and gas, and manufacturing need to know about layers of protection to operate a safe plant and meet regulatory compliance, and identifies the primary reason for failures.
View the Webinar: Layers of Protection in Process Safety Management
About the Presenter
Chet Barton is a TÜV Rheinland certified Functional Safety Engineer with over (30) years of experience in the Process Safety field. His experiences cover the petrochemical & refining, pharmaceutical, and aerospace industries, ranging from electrical and instrument technician roles to the role of controls systems engineer. He has been responsible for the specification, design, installation, testing, startup and maintenance of many power, process control, and safety systems. Chet leads Hargrove’s Team of seasoned and highly-trained SIS specialists and PHA facilitators, with senior members participating in international safety standard committees.
Chet has developed client standards, facilitated process hazard analysis (PHAs), and completed hundreds of LOPA projects for clients. He has also developed safety requirements and specifications, completed safety integrity level (SIL) calculations, and programmed and commissioned safety instrumented systems.
Recently Chet joined Control Global, a magazine exclusively dedicated to the global process automation market, to contribute to two process safety articles written by Executive Editor Jim Montague.
A Technical Engineer with a Minor in Psychology
“When I have the opportunity to present on workplace safety, I like to emphasize the importance of situational awareness,” Chet Barton, stated. “This involves pausing for a few minutes to think about what you’re doing, what you’re going to be doing, and what could happen. You should be looking around at your surroundings, the other people and equipment involved, and how what you’ll be doing might affect them.”
A job hazard analysis involves evaluating safeguards and equipping Teammates with the proper equipment and techniques to perform their job safely. “A job hazard analysis is very much like a process hazard analysis, just looking at things from a different perspective.”
Barton continued, “People think it’s kind of funny that I got a minor in psychology with a technical engineering degree, and I actually do, too. I originally got it because I thought it was an interesting field of study, and I enjoyed the classes, but there’s a segment of psychology called industrial psychology. This is the study of human behavior in the workplace, which was of particular interest to me. I later realized in my process safety work that much of what I deal with is actually human behavior, so it really does relate.”
Is Your Facility Protected?
Are the holes in your Swiss cheese resulting in incidents and consequences? Are you able to keep your plant personnel and the surrounding community and environment safe? Are you complying with OSHA regulations? Contact Hargrove’s safety specialists today for a consultation.